【Deviser Special Showcase Event – 2022】A ROSETTA VESSEL Model With Unique Specs!
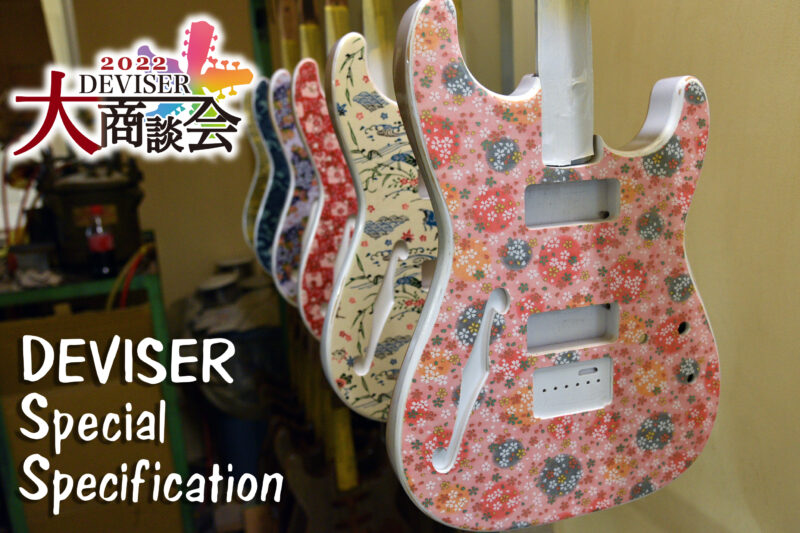
Discontinued in January of 2007, is the Deviser Special Specification【ROSETTA VESSEL】.
The popularity of the Rosetta series has been slowly growing on the second-hand market, and we have received many requests to restart production of this model.
We are pleased to announce the triumphant return of the -Deviser30th Anniversary- edition we originally made for last year’s “Deviser Special Showcase Event”.
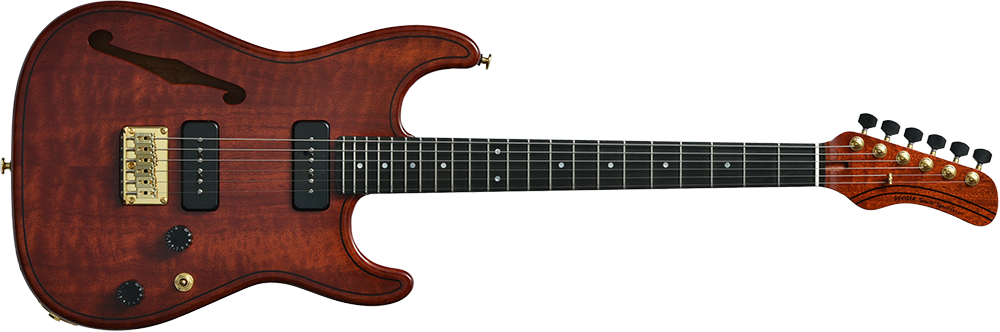
Last year we introduced many unique iterations of this fan-favorite model.
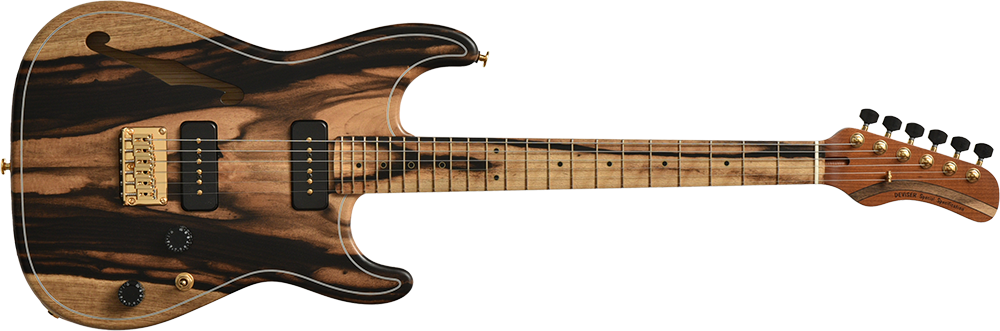
A model made from a large cedar that was felled by a torrential rain disaster at Shinmei-jinja Shrine in Otsu-machi, Gifu Prefecture!
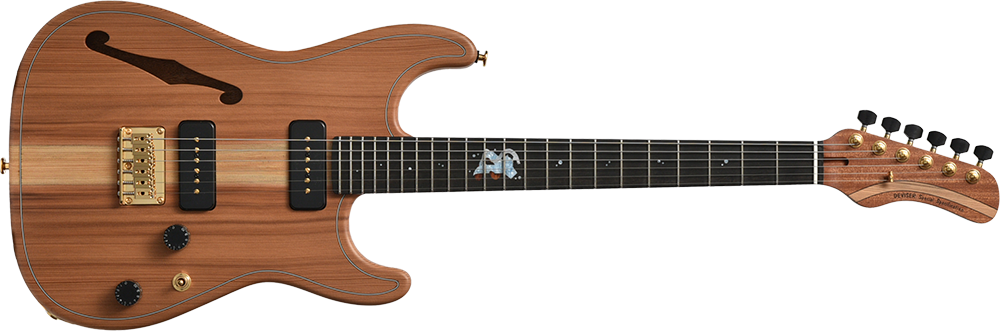
A Cherry blossom collaboration model with traditional craft Karuizawa carvings!
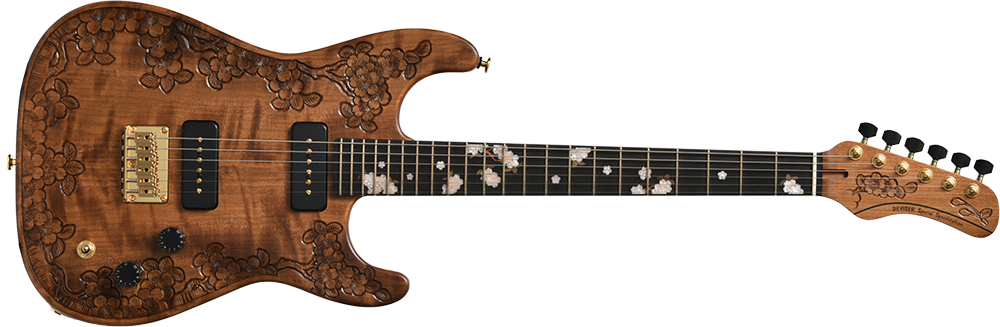
And many many more!
What kind of models will be presented at this year’s event then?
This time around, we bring you a particularly Japanese-inspired model!
It’s the -ROSETTA VESSEL WASHI “和紙”- Model!!
Tops decorated with Washi! But what IS Washi?
Washi (和紙) is a word composed of the character “和” meaning “Japan” or “Japanese-style”, and “紙” meaning “paper”, so in simple words, Washi is “Traditional Japanese Paper”. The term is used to describe paper that uses local fiber, processed by hand, and made the traditional way. Washi is made using fibers from the inner bark of the gampi tree, the mitsumata shrub, or the paper mulberry bush.
It is said to have originated around the 3rd or 4th century. As soon as paper records were started, the need for paper increased and production began, and it was later used as a material for crafts and cultural purposes.
Today, Japanese paper is used for diplomas, Japanese banknotes, and other items, and is probably a familiar material that everyone living in Japan has come into contact with at least once.
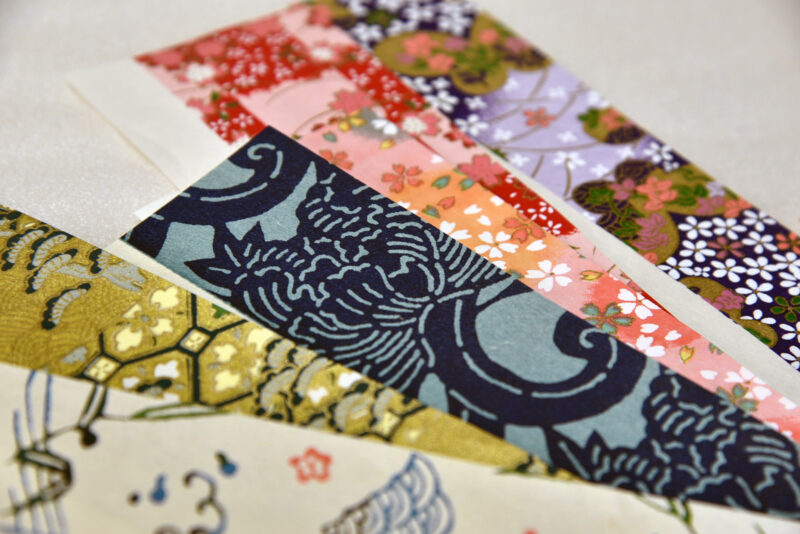
We have taken the challenge of making guitars incorporating Washi paper in the creation of our ROSETTA models starting back in the 2000s. Since those years, we’ve only produced 243 guitars in total, so you can imagine it isn’t an easy task.
Quick interview with the painting department, ROSETTA VESSEL Washi model!
More than 20 years have passed since then, and the level of guitar production and the skills of craftsmen have greatly grown!
We had an interview with Mr. Kajita of the Paint & Finish department at the Aska Workshop about the new Washi models produced by what’s now a more knowledgeable and experienced team of craftsmen!
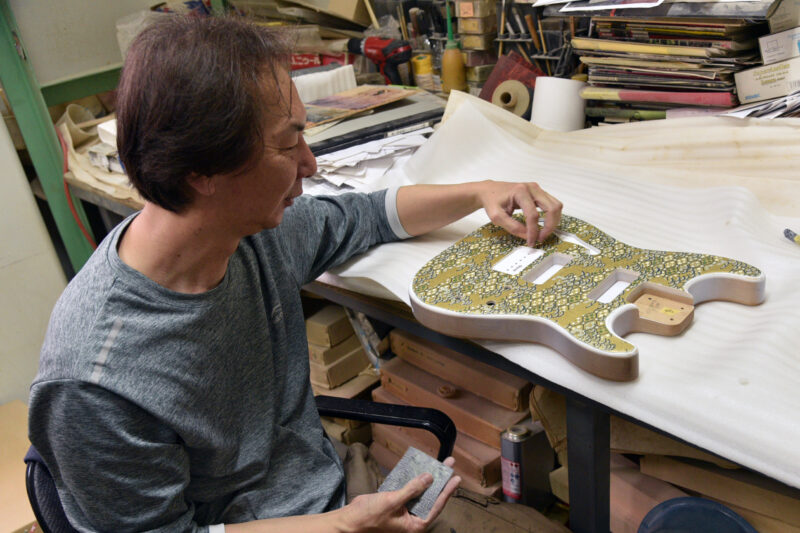
Interviewer:
A pleasure to meet you, sir. I hope you don’t mind if we jump right to it but, how are the Washi models coming along?
Kajita:
Well, as one would expect, visually, the result is great… But we wouldn’t call a “great” material.
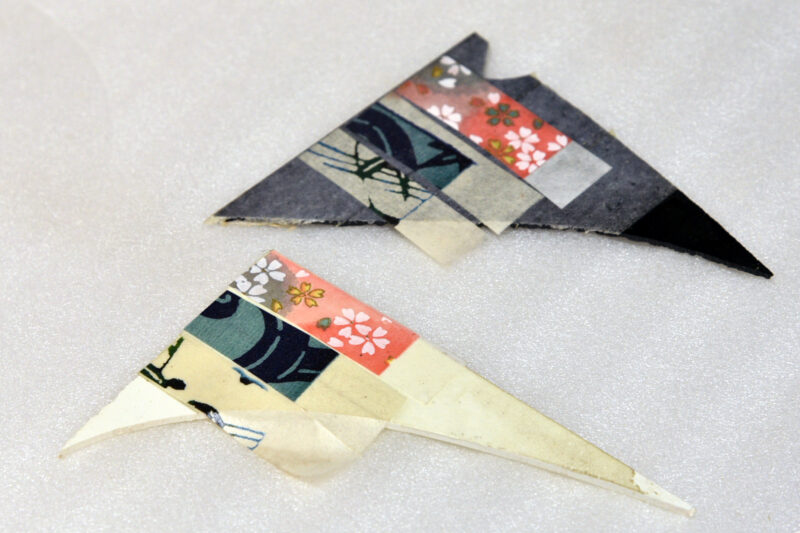
Interviewer:
How come? No matter where you look at them from they are really beautiful! What part of it isn’t great?
Kajita:
The making process is the part that isn’t great. Washi models are actually quite labor-intensive models to make. There are Washi papers with a black-ish pattern to it, and there are Washi papers with a white-ish pattern to it.
Especially with the white-ish pattern ones, the underlying color shows through, so it takes a lot of trial and error to make look just right.
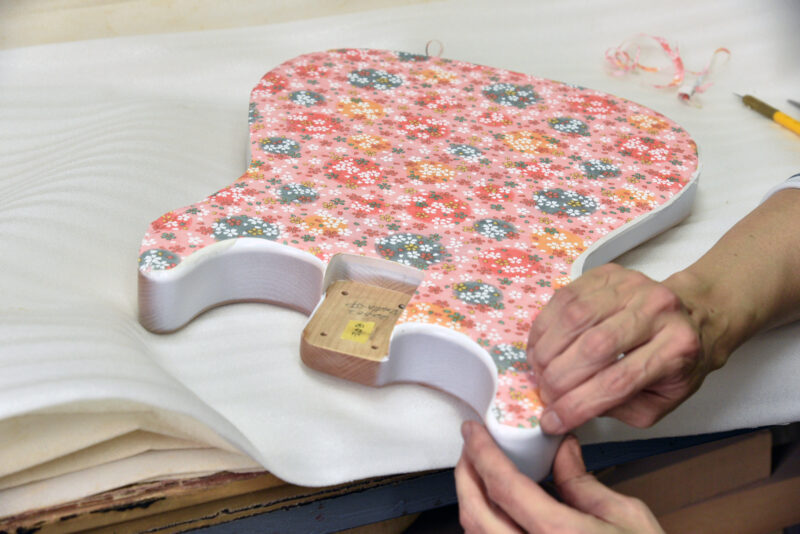
Interviewer:
I see! You meant it isn’t great from the perspective of the craftsman working with the material. It is true that Washi can have countless patterns. I can imagine it is a lot of work, but the results are undeniably beautiful!
Kajita:
We are just getting started.
From here, we will start to open up the counterbored holes for the pickups and the F-holes that are characteristic of ROSETTA VESSEL.
Interviewer:
Now you’ve got a familiar shape! From here you’re going to assemble in the neck and pickups, right?
Kajita:
It’s easy to forget because of how nice the Washi looks, but we haven’t painted the rest of the guitar yet- (laughs)
We’ll keep working on it from here.
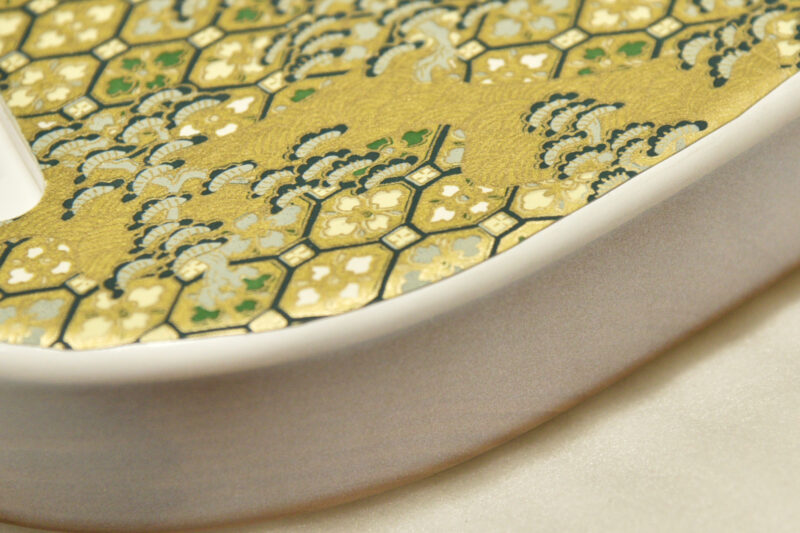
Kajita:
Washi is thick, so if we do the painting as is, the edges will end up being misshapen, to prevent that, the corners are shaved and smoothed out so that the change in height is as smooth as possible between the wood and the surface.
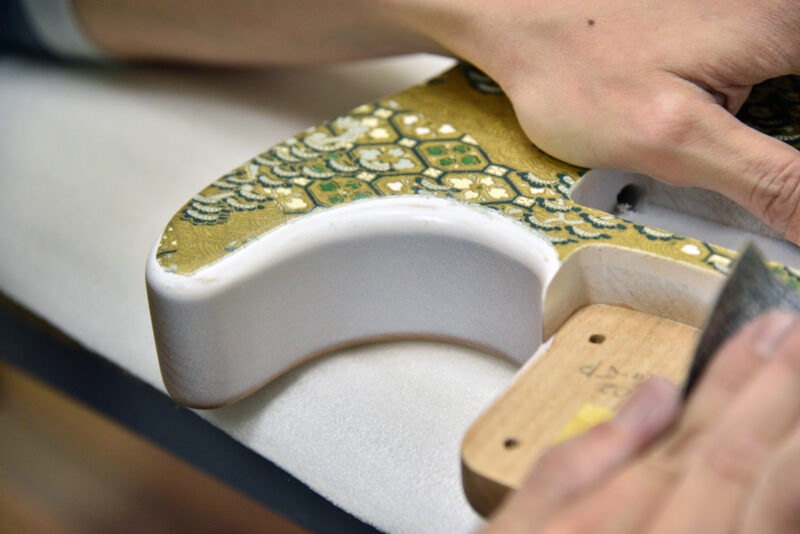
Kajita:
This is a very difficult task, especially since it is a part that is not usually done on ordinary models, and it is a world of a few tenths of a millimeter.
If you let your guard down here, you will be in a lot of pain later on…
Kajita:
At this point, a clear layer is finally applied.
This is finally the end of the preparation before the color is applied.
Interviewer:
This is where the real work begins, right?
What will the finish look like?
Kajita:
Well…
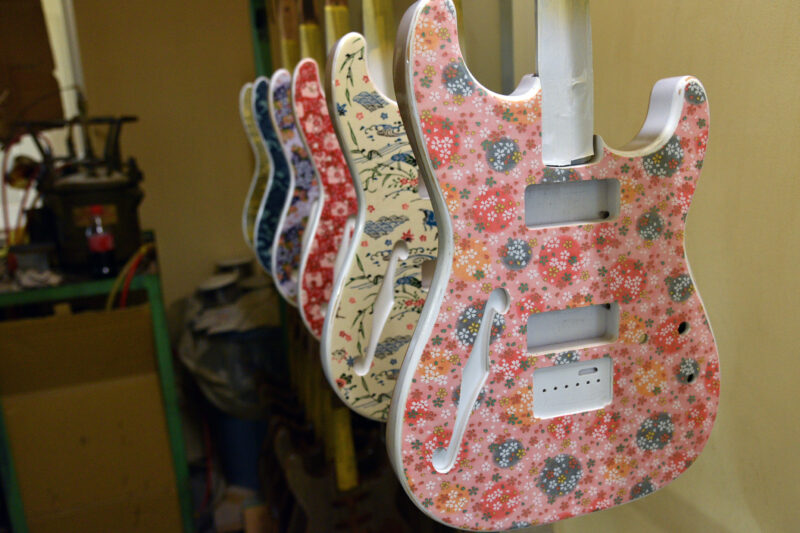
Please look forward to the Deviser Special Showcase Event – 2022!