About Thermowood
Introduction to Thermowood
A technique that simulates the natural aging process of wood
“Thermowood” is a wood processing method developed and mainly used in Finland for use in building materials. In recent years, interest in using this method to improve the acoustic characteristics of the wood and using it for guitar making has also appeared. The wood turns into a unique brown color when it is dried in an oxygen-free condition after being heated at a high temperature near 180°C. All images below are from necks made of maple wood, but normal maple and thermowood maple lined alongside one another so you can compare how much the color changes. with thermowood.
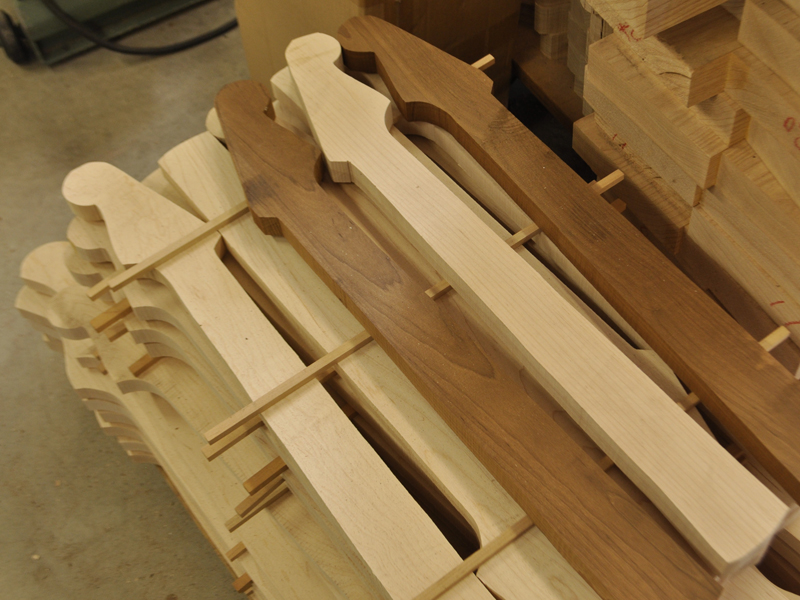
The advantages of this treatment are “dimensional stability” and “change in sound quality”. Normally, after the neck is built into the guitar and finished, it gradually dries up with time. What we call “vintage guitars” are guitars that had the chance to dry up throughout the years. This process gives the instrument a “withered” or “dried” sound that is very desired by many musicians.
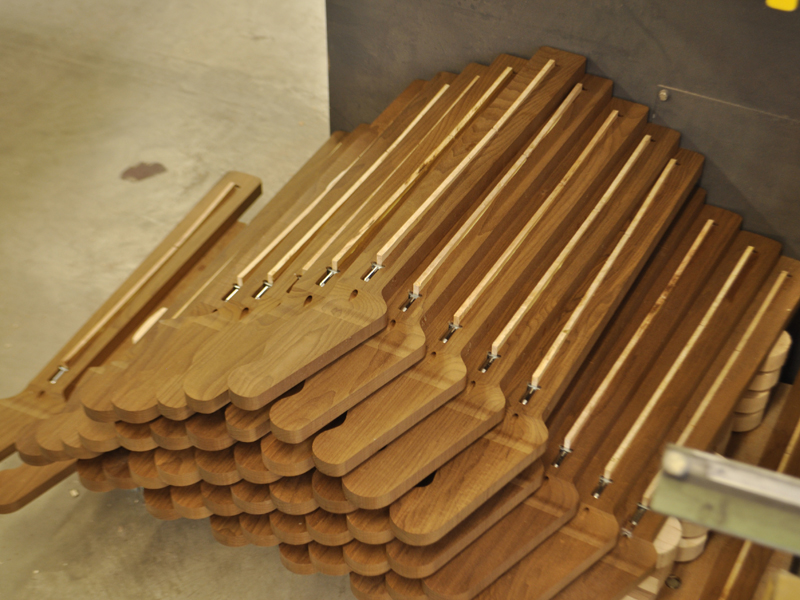
The neck material that has undergone the Thermowood treatment has less water content and less oil than the wood used for normal production. This gives us a similar result to that of a vintage guitar that has developed its wood throughout the years. By using this neck, which has been forced to undergo secular change, it reproduces a “new but vintage-like sound”. A kind of ideal guitar is completed for the player.
The Thermowood treatment is roughly divided into three stages
1. Drying process
The wood placed in a steam-filled device is first dried at a temperature of close to 100°C until the water content in the wood goes down to about 0%. This process takes about 18 hours.
2. Heat treatment process
After a certain period of time, the temperature is rapidly raised to a higher temperature (180℃-200℃). This lasts for about 10 hours.
3. Cooling/humidification process
The treatment is completed by adjusting the water content (moisture in the wood) of the material at room temperature. It takes about 15 hours.
We will refer to the materials in this process and various fields for reference. You could think “Why doesn’t the wood just ignite at those high temperatures near 200°C and burn down?”. Well, the trick is in the chamber where this takes place. It doesn’t burn even at high temperatures because that chamber is filled with water vapor and contains almost no oxygen, preventing any possible ignitions. It has been proven that wood that has undergone this treatment presents improved resistance to warping and twisting.
Wouldn’t you agree that this is really advantageous even if just using it for the neck of the instrument is a great idea? We think this is especially useful for those players looking to get that nice vintage sound from a brand new instrument!